
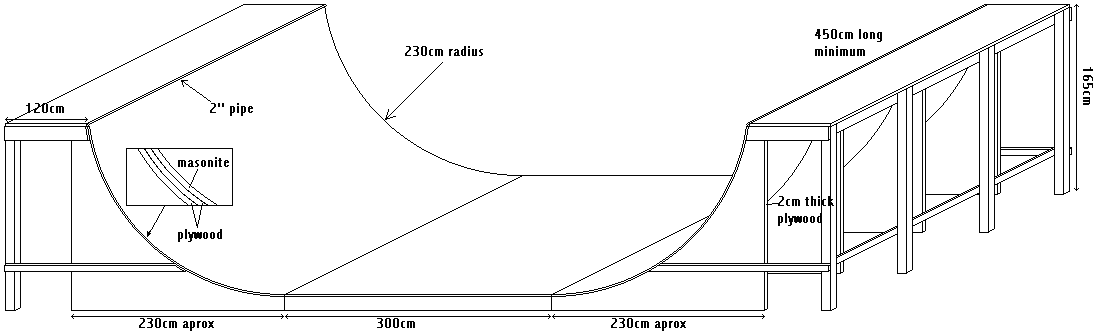
Nature enthusiasts enjoy viewing an abundance of waterfowl and shorebirds in the park’s scenic wetlands, as well as from the swimming beach and picnic areas along the lake. These wetlands are remnants of the Great Black Swamp, which once covered an area 120 miles long and 30-40 miles wide. The park also lies on the fringe of Ohio’s prairie marsh zone. Fall 2022 DNAP eNews - Prairie RestorationĮast Harbor is situated on a peninsula stretching into the waters of Lake Erie.
#2.5 FOOT MINI RAMP PLANS DRIVER#
And do it with a 3:1 excess of strength which should take care of variables like deciding to load something heavier, driver weight, bouncing, etc.Īctual channel would be stronger in proportion to the thickness of the flange. The ramp should hold a two axle item of 1000lb total weight that has equal weight on each wheel, and a space between wheels somewhat over 3 feet. Regular A36 steel should be good for 30,000psi or so. That's 10,000 psi, which is well within the capability of ordinary steel. Then a point load in the middle (like one axle) of 250 lb should give a tension of 30/3 * 250 or 2500lb. It's actually more, because the web takes some, but this is an estimate. the total area in tension can be assumed to be a quarter of a square inch. If you have a five foot ramp, and 3 x 1 inch channel 1/8 thick in the flange (which I don't remember if it even exists that thin). if you really just wanted to wing it then estimate by eye and start welding. You will have one on each side, so the total of two flanges for each ramp. It's just what I said, but do use channel, then the bottom and top flanges are the part that takes the load.
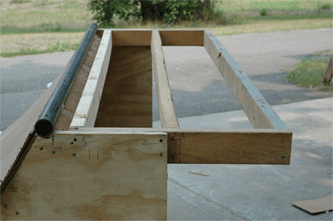
I did take some structural courses way way back, when I thought I might want to be an architect. Offhand that sounds like a bad idea, but the calculation will show it if so. Since you spoke of "thickness", it sounds like you want to run it up a piece of plate, or 2x stock laid on its wider side. Ramps tend to be self bracing due to their width. If so, then you need to look at the thing to see if the length to width ratio is too much, in which case you need to make the width effectively more by bracing. Sufficiently has to include any loads due to the skidloader bouncing on the ramp which it will do. Then you look at the capability of the material, and see if your actual strength exceeds the required strength sufficiently. Ends are not restrained for a ramp, no support due to that, they are just point supports. the height of the beam gives a lever arm around the "neutral axis", which allows you to figure the tension etc. If the beam is an I-beam, the area of the top or bottom can be assumed to be the resisting area. With any beam, the old school approach is to as a first step assume the load, and look at the tension and compression in the beam. The mechanical engineers will laugh at me. Even a formula (as long as it's not too complex) is fine as I'm not afeared of using pencil & paper.

So anyway, any help, either directly or via pointing me at a link or whatnot to help me figure out what I'm looking for would be most appreciated. The distance between front and rear tires is a little less than 3 feet (short wheelbase, huh?). My intended load will be this little skidloader I just picked up and the typical weight of it is about 2500 lbs. It just hasn't been necessary to figure this kind of stuff since over 30 years ago, and back then it was just in a physics class. I know that the most basic figuring would net a useful result and I'm a bit embarrassed that I don't know where to start already. Sure I want a little safety margin so it's not on the teetering edge of buckling, but no sense going nuts on that and I'm not schooled about moments of inertia and shear strength and all that fancy physics, hehe. The ramps have to be manipulated by human muscles and I'd like to minimize any damage to self. I can just overbuild it, but as you know thicker steel translates to more weight, and it would be nice to make it just handle the intended load safely but not so heavy to handle 3 times what will ever be on it. I thought some kind of calculator would pop up at the top of the google search list, but no love there so far. So I plan to make a pair of ramps - basically yer standard ladder style - 1 foot wide each, 8 feet long (maybe a bit shorter if that's too problematic) and essentially each of the ramps will be made from 2 pieces of angle iron at 8 feet long (4 total) with angle iron, channel or something not yet determined for the tread "web". The cross pieces mostly just give the tires something to bear on while the "rails" bear the brunt of the load itself. Yea I know it depends on the design, but say I was going to build it from 2"x2" angle iron for the length. I just want to figure out how thick my material ought to be for some trailer ramps. I've been searching the net without success.
